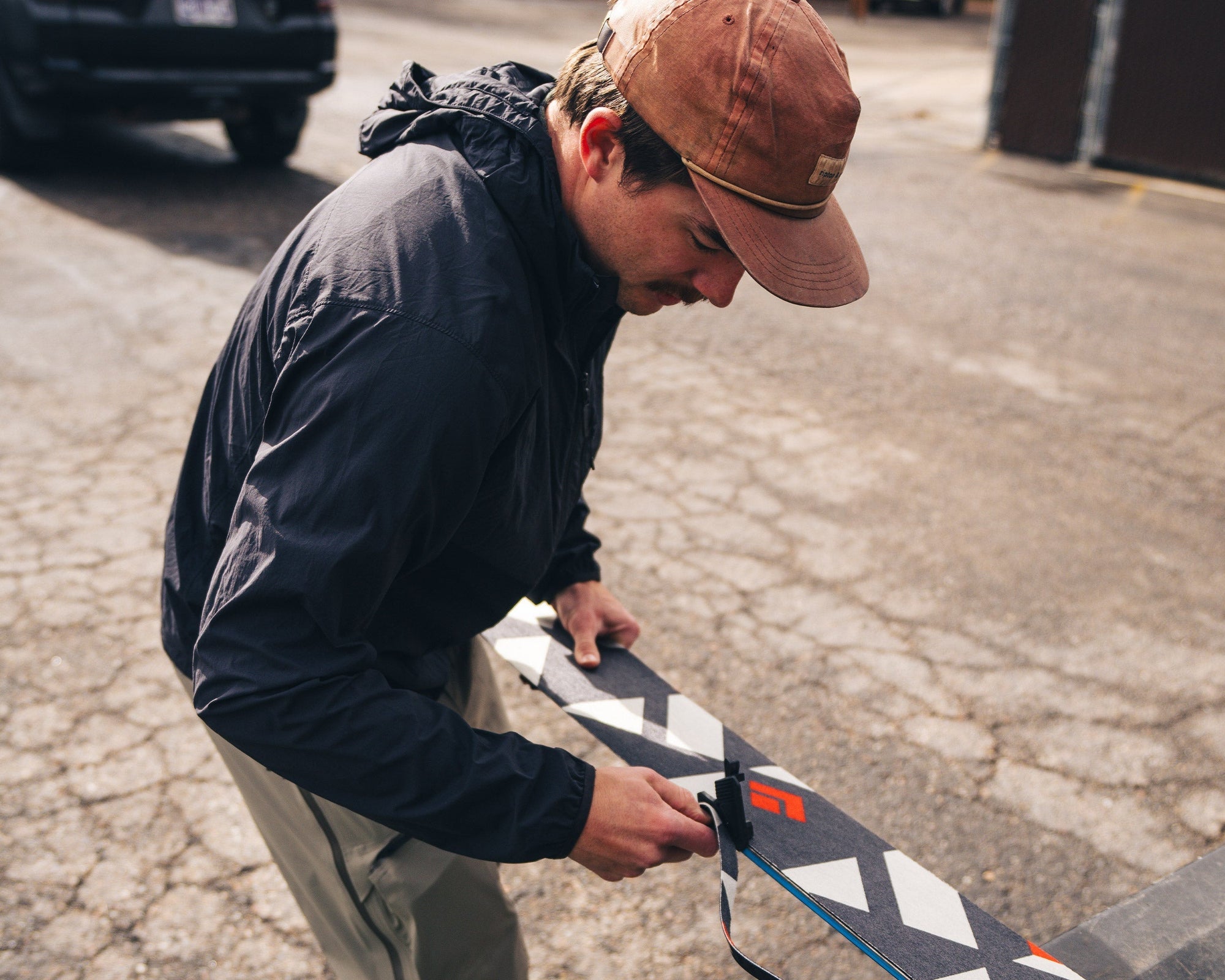
HOW TO TRIM YOUR BLACK DIAMOND SKINS
Watch and learn as our Field Test Coordinator runs you through a step by step...
Add $99.00 more to quality for free Shipping!
$0.00 USD
It's worth mentioning that as Kolin and his team were developing this post over the past few weeks (which is the culmination of years of testing and documentation), we became aware of some discussions in a couple online climbing forums and blogs filled with rumors and misinformation about BD crampons and the people who work here. We watched the discussion—dominated by a handful of posters with well-documented personal vendettas against us—devolve into a series of irrational personal attacks, lies paraded as insider knowledge, and misleading and bullying of fellow forum members who voiced support for BD or asked for facts to support the claims. As the vitriol became more and more erratic, personal and baseless, we realized it would be best not to engage in such dialogue that is unconstrained by facts or respect.
Fortunately, KP and his crew continued developing this post, and we feel this serves to bring all the facts to the table. This QC Lab provides the technical data and crucial manufacturing insights for climbers who want to be fully and properly informed on crampons: how they are designed, how they are built, the materials used, how they are tested, why they break, how often they break, and how to increase their lifespan.
We realize that to some people, to innovate is to disrupt; it makes them uncomfortable. This is nothing new. When we made the climbing world's first wiregate carabiner or carbon fiber ice tool, there were doubters who were spooked by the nonconformity and innovation of our designs and materials. And now? Those radical designs and revolutionary materials have become iconic standards of innovation in climbing equipment. Building our crampons out of stainless steel is just another step down that path of innovation.
Climbing is not merely our business—it's our life, it's our passion, it's what we do—and all of us here at Black Diamond Equipment are obsessively dedicated to innovating, designing and building the absolute best gear possible in support of you, our fellow climbers. Stainless steel crampons have become, by far, our best selling models of all time—a point of pride we share with every climber, from paid professional to weekend warrior, who uses our crampons. We appreciate your feedback, your vision, and your stoke, and are continually humbled by the summits and climbs you have achieved with our equipment.
Most crampons on the market adhere to the CE (EN893) and UIAA 153 requirements. These requirements include: minimum length of spikes, prevention against slippage, bending and breaking strength of spikes, strength of bails and retention system and strength of the frame. For a bit more insight into the CE and UIAA requirements for crampons, click here to go to the UIAA's webpage on safety standards.
As with all BD products, we are obsessively dedicated to designing and building the absolute best gear possible (which means going above and beyond CE and UIAA standards), so we have created a battery of testing machines and tests that our crampons need to go through before they hit the market, including: fatigue testing, material wear testing, ultimate strength testing, crampon balling testing, high and low temperature testing, salt spray testing, UV testing and, of course, the fun part: field testing.
Nearly every single manufacturer uses the same combination of the following processes: vertical front points are hot forged; frames and horizontal front points are stamped, laser cut, milled or water jet from sheet and then cold formed. We do the entire crampon manufacturing downstairs here at BD HQ, and it's cool to go down there and watch the process unfold.
A few years ago, Black Diamond switched from using chromoly steel to stainless steel for our crampons. The reason? Stainless, though roughly three times more expensive than chromoly, is less susceptible to rust, doesn't require toxic paint or powder coating, performs better and, as a bonus, looks cool. As climbers, we count on stainless steel in critical areas every day: most newer bolts and bolt hangers are stainless; cables, ball swages and many parts on cams are stainless; and many ice axe heads, spikes, crampon and ice tool components use stainless. But before we made the switch on our crampons, we did a ton of testing to verify material selection. As well as targeting all of the CE and UIAA requirements, we performed our battery of additional tests: wear testing, crampon balling testing, fatigue testing.
What did we learn about stainless?
Field Testing: We tested stainless steel crampon protos around the globe for more than two years, from single-pitch mixed rigs to multi-day Himalayan giants to free solos in the Canadian Rockies, by some of the top climbers in the game (as well as some of the top hacks in the game—myself included). Athletes, testers, and employees put the stainless steel protos through pitch after pitch of use and experienced significant improvements in several performance characteristics (see below).
Wear: In our field testing and point wear test comparison in the QC Lab, we saw improved point durability in the stainless we selected over our previously used chromoly. Point geometry and rust (see below) were also significant contributors to how quickly points became dull.
Fatigue: As noted in the previous QC Lab post regarding ice-tool picks, there is no official CE requirement for the fatigue life of crampons (or any climbing gear, for that matter). Fatigue life and optimizing the gear we make is extremely important to us, so, CE requirement or not, we designed and built our own crampon-specific cyclic machine (three actually) that test fatigue life (think: bending a coat hanger back and forth over and over until it breaks). Our goal was to determine if there was a significant difference in fatigue life based on material selection, geometry specifics, varying the loads, placement of loads, frequency of loads, etc. We cut old geometry out of stainless, we cut new geometry out of chromoly, we tested old Black Diamond products, other manufacturers products, and many iterations of prototypes—all in order to get a true understanding of where geometries, materials and the competition all stacked up as it pertains to cyclic durability. Overall, we tested hundreds of crampons, and continue to test as new styles and various performance characteristics adjustments are developed.
Below is a graph that shows a variety of front-point cyclic fatigue comparisons of BD Cyborg and Sabretooth crampons in both stainless and chromoly. What this test showed us was that, in regards to fatigue life, stainless steel was in the same ballpark as chromoly.
Even given all of the design work, material selection and testing that Black Diamond and most other manufacturers perform, under certain circumstances—and as with picks and most any gear—crampons won't last forever. Crampons can and do wear out or break in the field—they always have. Points can become dull and eventually too short from continuous sharpening, bails can get tweaked, bent or rusted, points can bend or break from being torqued in a crack or heavily, single-point loaded during climbing or even walking (often while descending on hard ice or rocks), and points, center bars or crampon frames can ultimately break from the continuous pounding from metal fatigue.
In 2001, the British Mountaineering Council created a pamphlet to help educate climbers on gear, its uses, limitations, gear maintenance and inspection. Here's an excerpt from the pamphlet regarding crampons:
Crampons take an incredible amount of punishment – a climber carrying a heavy rucksack and walking over rock or boulders transfers a large force onto the points of the crampon. (For the technically minded the impact force can be around 3kN, which on rough terrain might be shared by only two or three of the points!). Also the crampon bends slightly, even on the stiffest boot, and this happens on every step.
On a ten-mile walk a crampon could experience 10,000 bending cycles. Metal will break if cold enough and either bent with sufficient force (brittle fracture) or flexed back and forward enough times (fatigue failure). The surprising thing is not that some crampons break but rather that most crampons don't break – a testament to our equipment manufacturers.
Click here to read various reports—albeit ones that are a bit dated—that the British Mountaineering Council posted on their website about crampon and all kinds of other gear field breakages.
The BMC pamphlet reports only 31 crampon field failures over a 15-year period. Not many. But remember that this information is from more than a decade ago. The current reality is that gear makers are pushing the limits of design (i.e., making gear lighter and more performance oriented, which usually comes at a cost of durability) and climbers are being harder and harder on gear because climbing styles and difficulty have changed so much in recent years.
Crampons break; they always have. No manufacture has a magic material or process to produce an unbreakable crampon. Every company has warranty returns, but all I will cover here are crampons that have been returned to Black Diamond. Our data includes everything from a broken frame or center bar to a slightly frayed strap to an ABS plate that has baked and melted in a car fire. All inclusive, our historical return rate for crampons is less than 0.1%. Specifically, crampon warranty return rates were around 0.06% for the eight-year period prior to using stainless steel, and around 0.02% since switching to stainless in 2009— as you can see in the chart below. We have rarely ever seen vertical front point crampons returned (remember that 2x6 analogy), so if we divide the warranty return rate down by model, it creeps close to 0.2% for technical crampons with horizontal front points (not shown specifically in this graph).
Every piece of climbing gear returned to BD Warranty eventually comes across my desk. We in the QC Lab analyze the returns and complete a comprehensive investigation. We treat every return as a serious opportunity to understand what happened, how it happened, and what's going on in the field, as well as an opportunity to improve our products through refinements and meaningful design tweaks. Even though all of our crampons exceed all international standards, we do not hesitate to improve and optimize them based on real-world usage.
Historically here at BD, we would see a few random crampon returns for frayed webbing, plastic toe straps getting beat, bent front points or tweaked down-points. Sometimes we would see bent or broken rear down-points—usually from people descending hard ice or rocks and the heel down-points taking the brunt of the load. And sometimes we have seen broken crampon frames or center bars—often returned from trekking companies whose crampons see tons of mileage on glaciers, usually with people wearing really soft boots that flex a lot and cause a bending load on the frame.
Crampons
I don't think we've ever seen a vertically oriented front point crampon frame break, but we have seen horizontally oriented front point frames break. As a general rule beefier crampons with vertical front points performed better in cycle fatigue than lighter crampons with horizontal front points. This should be no surprise. So if you are planning on doing a lot of front pointing on water ice or you're an Alpine MOG that tips the scales over the 90kg level, you will best be served with a vertical front point crampon.
We wanted to be able to put some actual numbers to the difference in fatigue life, so we did a comparison on our homemade cyclic machine that represents repeated front pointing. And, as always, we not only tested our own current-model crampons but also other manufacturers.
As you can see, pretty much across the board, vertically oriented front points do better than horizontal. Once again, this increased durability is from the vertical oriented front points increasing stiffness and being able to take more abuse before fatigue.
Boots and Center Bars
Proper boot selection and fit to the crampon is critical in optimizing performance and maximizing lifespan. If you're using a boot that has lots of flex, a flexible center bar allows the crampon to move with the boot, thus reducing the bending load forces on the front frame of the crampon.
We wondered how different boot and center bar combinations affected the lifespan of crampons—so we tested it. We ended up comparing how many cycles a crampon could take before failure, depending on which boot was used:
As well as, which center bar was selected (rigid or flexible)
(Note: This test doesn't directly correlate to any actual real world pitches of ice or miles of walking. It must be taken as a direct comparison within it's own dataset.)
Watch and learn as our Field Test Coordinator runs you through a step by step...
Watch and learn as our Field Test Coordinator runs you through a step by step process of trimming and setting up any STS-style Black Diamond skin.
Every climber has a few lines they dream about. Whether inspired or haunted—or sometimes both—these...
Every climber has a few lines they dream about. Whether inspired or haunted—or sometimes both—these lines can push us beyond what we thought we were capable of, in turn teaching us who we really are. BD Ambassador Ethan Salvo recently restructured his entire life to focus on two climbs that pulled him into the void with only one way out … getting to the top. This is his story of sending Dreamcatcher and becoming the first Canadian to climb V16 in the same week.
BD Athlete Connor Herson spent as many weekends as possible in the Valley this spring...
BD Athlete Connor Herson spent as many weekends as possible in the Valley this spring during a grueling quarter at Stanford. The objective? Ground up, in-a-day ascents.
Follow Hillary in this documentary film capturing her record-breaking ascent of Europe’s tallest peak.
BD Athlete Seb Bouin takes us back to his home crag of Pic Saint-Loup where...
BD Athlete Seb Bouin takes us back to his home crag of Pic Saint-Loup where he establishes the true king line of the cliff—Wolf Kingdom.
A film documenting the often-overshadowed bouldering of Yosemite climbing, where jedis like BD Athlete Carlo...
A film documenting the often-overshadowed bouldering of Yosemite climbing, where jedis like BD Athlete Carlo Traversi have spent years learning to harness the force.
BD Athlete Hazel Findlay shares her tips for returning to the climbing life for new...
BD Athlete Hazel Findlay shares her tips for returning to the climbing life for new mothers.
A film documenting the first flash ascent of El Capitan by BD Athletes Babsi Zangerl...
A film documenting the first flash ascent of El Capitan by BD Athletes Babsi Zangerl and Jacopo Larcher.
BD Athletes Babsi Zangerl and Jacopo Larcher share their story of climbing one of the...
BD Athletes Babsi Zangerl and Jacopo Larcher share their story of climbing one of the world’s most mythical trad routes.
BD Athletes Aaron Mulkey and Yannick Glatthard take the new Hydra into the backcountry of...
BD Athletes Aaron Mulkey and Yannick Glatthard take the new Hydra into the backcountry of Montana in search of steep ice and mixed climbing.
Follow Dorian Densmore and Mya Akins for a month-long, exploratory mission in the Chugach Mountains.
Two BD legends walk into the Valley. What happens next? Watch and see.
With ski season kicking off, the QA Lab crew dives deep into the world of...
With ski season kicking off, the QA Lab crew dives deep into the world of electromagnetic interference and how it can affect backcountry safety.